-
01Customer Satisfaction
Through the contract review and product evaluation, we can know the customer needs and requirements of the laws and requirements. We also implement the customer satisfaction procedure to make them satisfied
-
02Continued Improvement
Through various management techniques, such as the project management, Lean Manufacturing (LM), and 6-Sigma, we can improve the quality, and continue improvement by auditing and various statistics
-
03Quality First
We achieve the quality first goal through quality planning, process control, and measurement monitoring to ensure quality
-
04Get to the Bottom of Issues
Through various methods, such as the quality feedback form, customer complaints, 6-Sigma, and Lean Manufacturing (LM), we can make a detailed analysis of issues and resolve them
-
05Employee Participation
Perform improvement through the organizational responsibilities and cross-functional operation mode
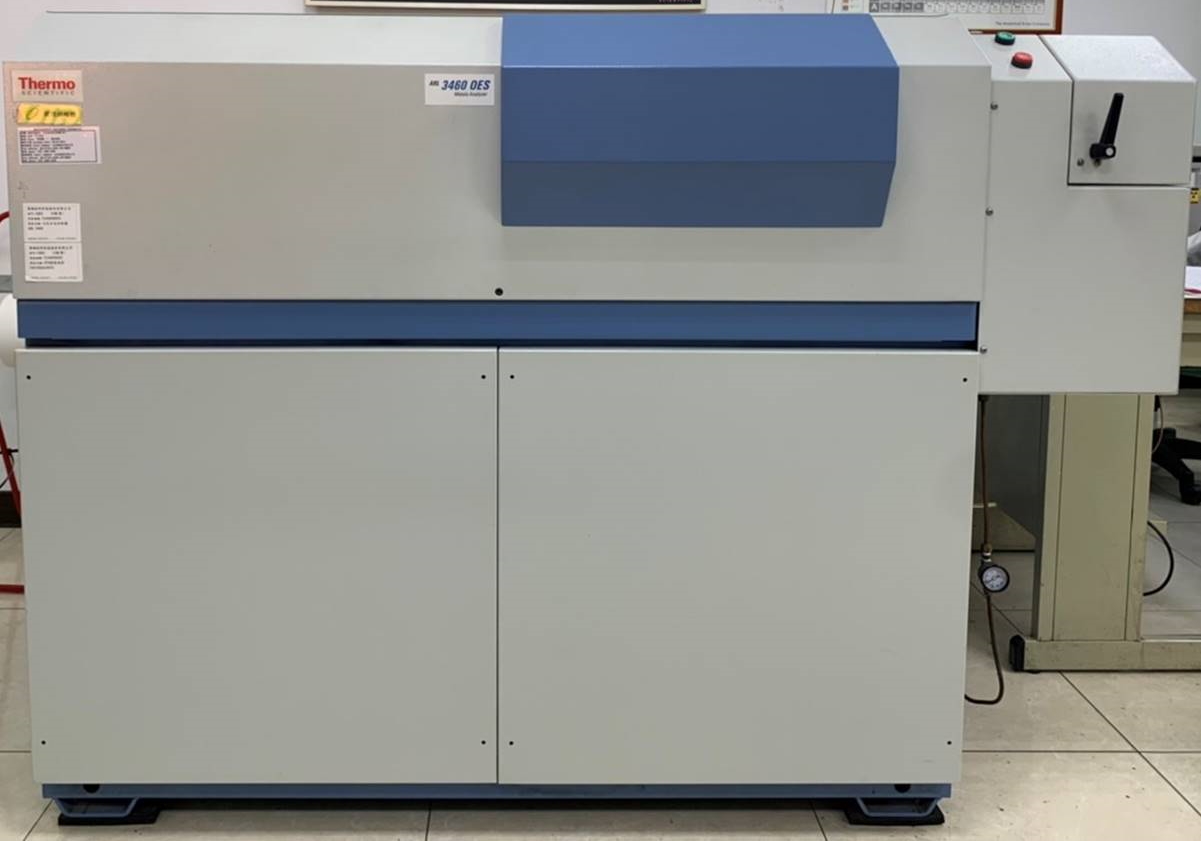
- Carbon, sulfur, oxygen, nitrogen and hydrogen testing via combustion or inert gas fusion techniques
- Spark emission Spectrometry analyze
- X-ray fluorescence analyze
- Inductively Coupled Plasma Spectrometry
- Portable-XRF
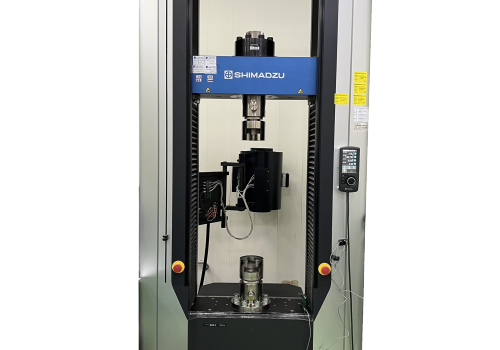
- Tensile test (ambient temperature /elevated temperature)
- Stress rupture test
- Impact test (ambient temperature / low-temperature)
- Hardness test (Brinell / Rockwell / Vickers, etc.)
- Metallurgical test
- Scanning electron microscope test
- Energy-dispersive X-ray spectrometer test
- Specimen machining
- Specimen heat treatment
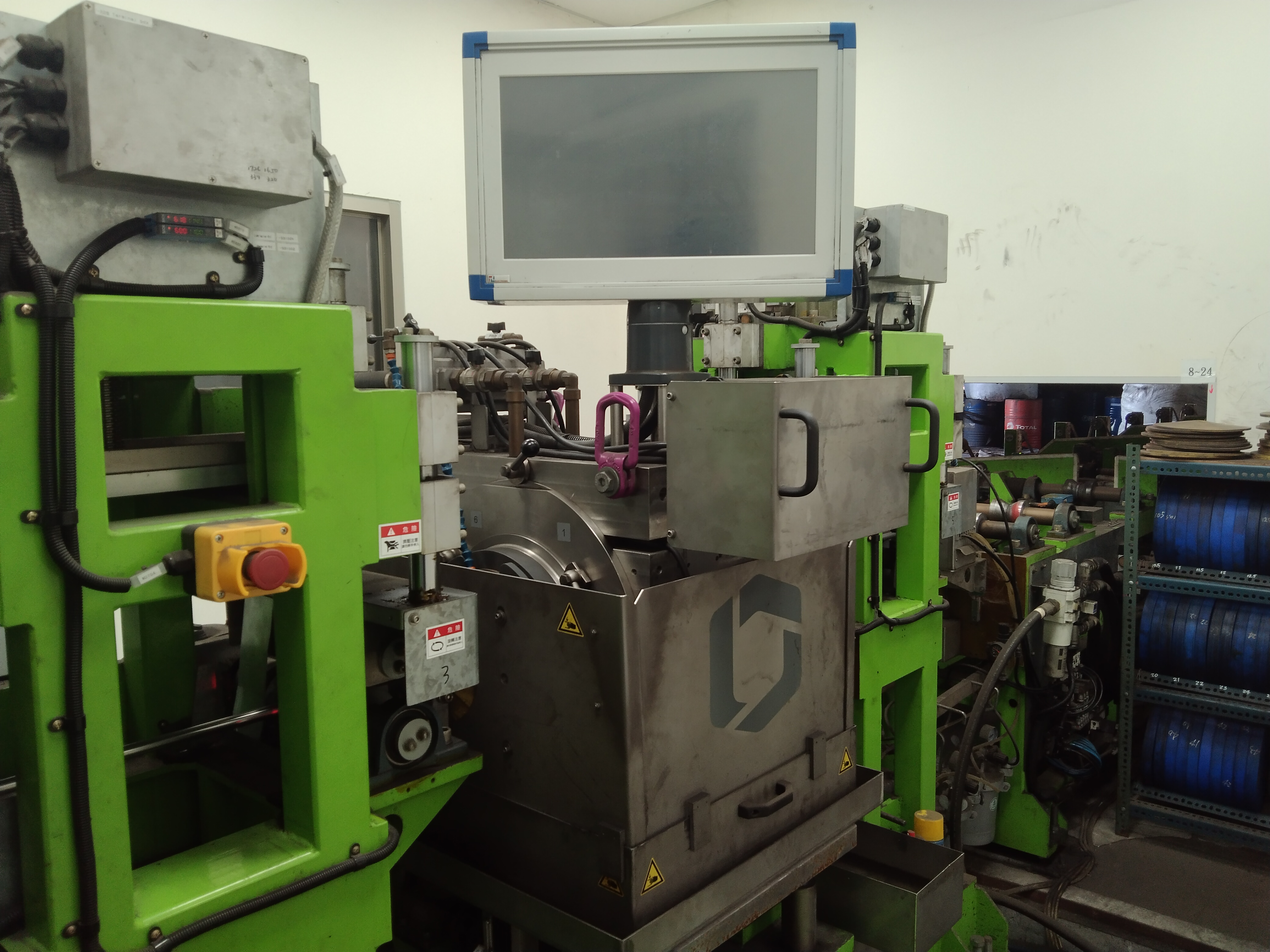
- Ultrasonic flow detection: Contact / immersion (traditional and phased array)
- Magnetic particle testing (fluorescence)
- Eddy-current testing
- Liquid penetrant testing
- Roughness testing
- Optical profile projection testing
- Height gage testing
- Portable-XRF
Select an item